ERP vs. Traditional Business Management Which Wins?
Defining ERP and Traditional Business Management
Understanding the differences between Enterprise Resource Planning (ERP) systems and traditional business management approaches is crucial for businesses seeking to optimize their operations. This comparison will illuminate the core functionalities, historical evolution, and key characteristics of each, allowing for a more informed decision regarding which approach best suits specific organizational needs.
Enterprise Resource Planning (ERP) Systems Defined
Enterprise Resource Planning (ERP) systems are integrated software applications designed to manage and integrate a company’s core business processes. These processes can include product planning, development, manufacturing, sales and marketing, and customer service. A core function of ERP is to centralize data from various departments, providing a single source of truth for improved decision-making and enhanced operational efficiency. This centralized system streamlines information flow, reduces data redundancy, and improves overall visibility across the organization. Examples of popular ERP systems include SAP, Oracle, and Microsoft Dynamics 365.
Characteristics of Traditional Business Management Approaches
Traditional business management approaches, in contrast to ERP systems, often rely on disparate, independent systems and manual processes for managing different aspects of the business. Data is frequently siloed within individual departments, leading to information discrepancies and difficulties in achieving a holistic view of the organization’s performance. Communication and collaboration between departments can be hampered by the lack of integrated systems. Decision-making often relies on incomplete or outdated information, potentially hindering strategic planning and operational effectiveness. Traditional approaches typically involve extensive manual data entry, increasing the risk of errors and reducing overall efficiency.
Comparing and Contrasting Core Functionalities
Feature | ERP Systems | Traditional Business Management |
---|---|---|
Data Management | Centralized, integrated database | Decentralized, siloed data |
Process Integration | Highly integrated business processes | Fragmented, independent processes |
Information Flow | Real-time, seamless information flow | Slow, often delayed information flow |
Decision-Making | Data-driven, informed decisions | Decisions based on incomplete or outdated information |
Efficiency | Improved efficiency through automation | Lower efficiency due to manual processes |
Scalability | Highly scalable to accommodate growth | Limited scalability, often requiring significant changes to adapt |
Historical Context and Evolution of ERP and Traditional Business Management
Traditional business management practices have evolved organically over centuries, adapting to changing business environments and technological advancements. Early forms involved simple accounting systems and manual record-keeping. The development of computers led to the creation of individual departmental systems, but these often lacked integration.
The evolution of ERP systems began in the 1960s with Material Requirements Planning (MRP) systems focused on production planning. Over time, these systems expanded to encompass more business functions, culminating in the integrated ERP systems we see today. The shift towards ERP reflects a growing need for real-time information and efficient integration across various business functions in response to increasingly complex and globalized markets. The adoption of ERP has accelerated in recent decades, driven by advancements in computing power, networking capabilities, and the demand for improved business agility.
Cost and Implementation
Implementing either an ERP system or sticking with traditional business management methods involves significant financial considerations. The initial investment, ongoing maintenance, and potential hidden costs can vary dramatically, influencing the overall return on investment (ROI) for each approach. A thorough cost-benefit analysis is crucial for making an informed decision.
Initial Investment Costs
The initial investment for an ERP system is considerably higher than for traditional methods. ERP implementation involves software licensing fees, often substantial depending on the scale and features required, consultant fees for system design, implementation, and training, hardware upgrades (servers, workstations, network infrastructure) may be needed to support the new system, and data migration costs associated with transferring existing data into the new ERP system. Traditional methods, conversely, often rely on existing software and infrastructure, resulting in lower upfront costs. However, this might involve purchasing individual software applications (like accounting, CRM, inventory management) separately, potentially leading to integration challenges and higher long-term costs. For example, a small business might spend $10,000 on individual software licenses for various departments, while a comparable ERP implementation could cost upwards of $50,000 to $100,000, depending on the size and complexity of the business.
Ongoing Maintenance and Operational Costs, ERP vs. Traditional Business Management: Which One Wins?
Ongoing costs for ERP systems include software maintenance fees (updates, bug fixes, support), ongoing consultant fees for ongoing support and customization, and the salaries of IT staff dedicated to managing and maintaining the ERP system. Traditional methods might involve lower software maintenance costs, as individual software packages usually have smaller maintenance fees. However, the lack of integration can lead to manual data entry and reconciliation, which can significantly increase labor costs in the long run. For instance, reconciling data across multiple spreadsheets and databases in a traditional system might require significant staff time, whereas an integrated ERP system automates this process, reducing labor costs.
Potential Hidden Costs
Both ERP and traditional systems carry potential hidden costs. For ERP, these include unforeseen customization needs (requiring additional consultant fees), integration challenges with legacy systems, and the cost of employee retraining and resistance to change. For traditional systems, hidden costs might include the escalating costs of managing data inconsistencies across different systems, the cost of resolving data discrepancies, and lost productivity due to inefficient workflows and manual processes. For example, a poorly planned ERP implementation could result in project delays and cost overruns due to unforeseen integration issues, while a traditional system relying on multiple disparate databases could lead to significant time wasted reconciling data.
Cost-Benefit Analysis Framework
A robust cost-benefit analysis should consider both short-term and long-term costs and benefits. This includes:
- Initial Investment: Compare the upfront costs of ERP implementation versus the costs of acquiring and integrating individual software applications in a traditional system.
- Ongoing Costs: Analyze the annual costs of software maintenance, IT support, and employee time for both approaches.
- Benefits: Quantify the benefits of each approach, such as improved efficiency, reduced errors, better decision-making, enhanced customer satisfaction, and increased revenue. For example, estimate the time saved by automating processes, the reduction in inventory holding costs, or the increase in sales due to improved customer service.
- Risk Assessment: Assess the potential risks associated with each approach, such as implementation failures, data loss, and integration challenges. Assign probabilities and potential financial impacts to these risks.
- Return on Investment (ROI): Calculate the ROI for each approach by comparing the total costs and benefits over a defined period (e.g., 3-5 years). The approach with the higher ROI should be favored.
The formula for ROI is: (Total Benefits – Total Costs) / Total Costs * 100%
Scalability and Flexibility: ERP Vs. Traditional Business Management: Which One Wins?
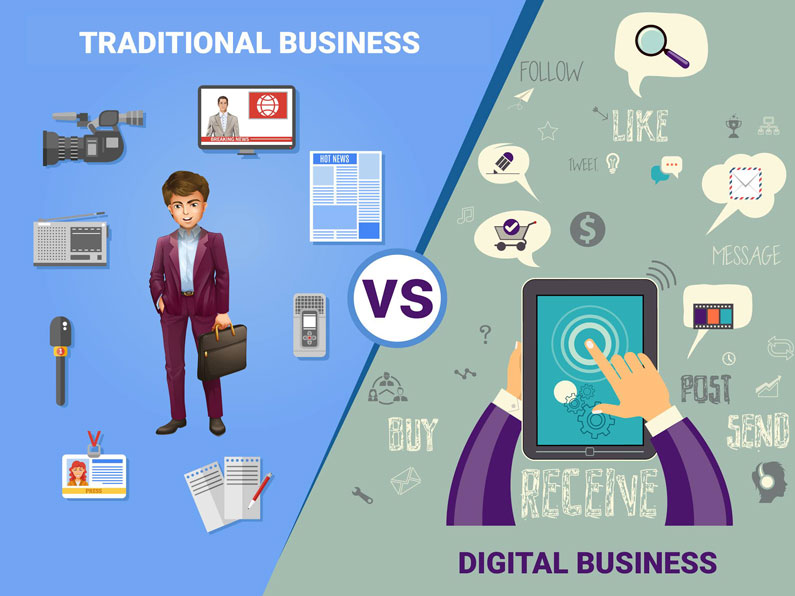
Choosing between an ERP system and traditional business management often hinges on a company’s growth trajectory and adaptability needs. Scalability and flexibility are crucial factors determining which approach best suits a particular organization’s long-term strategy. While both offer avenues for growth, their approaches and limitations differ significantly.
ERP systems and traditional business management approaches exhibit contrasting characteristics regarding scalability and flexibility. ERP systems, by design, offer a more structured and integrated approach to growth, while traditional methods often rely on ad-hoc solutions and incremental adjustments. This difference impacts how efficiently each approach can handle expanding operations and adapt to evolving market demands.
ERP System Scalability and Flexibility
ERP systems are inherently designed for scalability. Their modular architecture allows businesses to add functionalities and user licenses as needed, accommodating growth in terms of both data volume and user base. This scalability is often achieved through cloud-based deployments, which provide elastic resources that can be adjusted on demand. Furthermore, ERP systems offer flexibility through configuration options and customization capabilities, allowing businesses to tailor the system to their specific workflows and processes. However, extensive customization can increase complexity and cost. For example, a rapidly growing e-commerce company might start with a basic ERP system for inventory management and order processing. As it expands into new markets and product lines, it can seamlessly add modules for customer relationship management (CRM), supply chain management (SCM), and advanced analytics, all within the same integrated platform. Limitations arise when the chosen ERP system lacks the specific functionalities needed for a business’s unique requirements, necessitating expensive custom development or a switch to a more suitable system.
Traditional Business Management Scalability and Flexibility
Traditional business management approaches, often characterized by disparate systems and manual processes, present a different picture. Scalability in this context typically involves adding more resources—more employees, more software licenses for individual applications, and more physical infrastructure. This can be less efficient and more costly than scaling an integrated ERP system. Flexibility, while possible, often requires significant effort and time. Adapting to changing business needs might involve integrating new software solutions, retraining employees, and re-engineering existing workflows. A small bakery, for instance, might initially manage its operations using spreadsheets and basic accounting software. As it expands, it may add point-of-sale (POS) systems, inventory management software, and potentially a dedicated accounting package. However, integrating these disparate systems can be challenging, leading to data silos and inefficiencies. The lack of integration limits the overall efficiency and the ability to gain a holistic view of the business. The scalability limitations become more apparent as the business grows significantly, requiring more complex and integrated systems that are difficult to implement within a traditional framework.
Examples of Successful Scaling
Many large corporations have successfully scaled their operations using ERP systems. SAP, Oracle, and Microsoft Dynamics 365 are examples of ERP solutions that power the back-end operations of countless global enterprises. These systems allow businesses to manage complex supply chains, global operations, and vast amounts of data efficiently. On the other hand, some companies have successfully scaled using traditional methods, but often this involves a significant investment in infrastructure, personnel, and custom software development. This approach is often more challenging and less cost-effective for businesses aiming for rapid growth. Successfully scaling with traditional methods usually relies on strong internal processes and a very clear understanding of the company’s growth trajectory and future needs.
Limitations of Scalability and Flexibility
The scalability of ERP systems can be limited by the system’s inherent architecture and the vendor’s capacity to provide the necessary resources. Highly customized ERP implementations can become difficult to maintain and upgrade, hindering scalability. Traditional approaches, while flexible in the sense that they allow for piecemeal solutions, suffer from integration challenges, data silos, and a lack of a unified view of the business, ultimately limiting their scalability and long-term efficiency. The cost of integrating numerous disparate systems can easily outweigh the cost of implementing a well-chosen ERP system.
Integration and Data Management
The ability to seamlessly integrate data and manage it effectively is crucial for any business, regardless of its size or management approach. This section compares the data integration capabilities, security measures, potential challenges, and best practices for data management in both ERP and traditional business management systems. Understanding these differences is key to determining which approach best suits a specific organization’s needs.
ERP systems and traditional business management methods differ significantly in their approach to data integration and management. Traditional systems often rely on disparate, independent applications, leading to data silos and integration challenges. In contrast, ERP systems are designed from the ground up to integrate data from various business functions into a central repository. This fundamental difference significantly impacts data accessibility, analysis, and overall business efficiency.
Data Integration Capabilities
ERP systems offer superior data integration capabilities compared to traditional methods. They provide a centralized database that allows different departments (finance, sales, human resources, etc.) to access and share information seamlessly. This eliminates the need for manual data entry and reduces the risk of errors. Traditional systems, however, often involve manual data transfer between separate applications, a process that is time-consuming, error-prone, and inefficient. For example, a sales team using a CRM system separate from an accounting system would need to manually input sales data into both systems, creating opportunities for discrepancies and delays. ERP systems automate this process, ensuring data consistency and accuracy across all departments.
Data Security and Privacy
Data security and privacy are paramount concerns for any business. Both ERP systems and traditional methods offer varying levels of security, but ERP systems generally provide more robust security features due to their centralized architecture. A well-implemented ERP system allows for granular access control, enabling organizations to define specific user permissions and restrict access to sensitive data. This reduces the risk of unauthorized access and data breaches. Traditional systems, due to their decentralized nature, may present more vulnerabilities if security protocols are not consistently implemented across all applications. Regular security audits and updates are crucial for both approaches, but the centralized nature of ERP systems simplifies the management of security policies and procedures.
Potential Data Silos and Integration Challenges
While ERP systems aim to eliminate data silos, challenges can still arise. Poorly implemented ERP systems or a lack of proper data governance can lead to data inconsistencies and integration problems. For instance, if data isn’t properly mapped and standardized during the ERP implementation process, discrepancies can occur between different modules. Traditional systems, by their very nature, are prone to data silos. Each application operates independently, creating fragmented data and hindering a holistic view of the business. A lack of communication between departments further exacerbates this issue, making it difficult to track key performance indicators (KPIs) and make informed business decisions. For example, a marketing department might have customer data separate from sales data, preventing a complete understanding of customer behavior and marketing campaign effectiveness.
Data Management Best Practices
Effective data management is essential for both ERP and traditional systems. For ERP systems, this involves establishing clear data governance policies, ensuring data quality through regular audits and cleansing, and implementing robust security protocols. Regular training for employees on data usage and security best practices is also crucial. For traditional systems, the focus should be on establishing data integration strategies, such as using ETL (Extract, Transform, Load) tools to consolidate data from different applications. Standardizing data formats and creating a central data repository, even if it’s a less sophisticated system than an ERP’s, can significantly improve data management. Regular data backups and disaster recovery plans are also essential for both approaches to ensure business continuity in case of data loss or system failure.
Workflow and Automation
Workflow and automation represent a crucial difference between ERP systems and traditional business management approaches. Traditional methods often rely on manual processes and fragmented systems, leading to inefficiencies and delays. In contrast, ERP systems offer robust automation capabilities, streamlining workflows and significantly boosting productivity. This section will compare the automation capabilities of both approaches, highlighting their impact on efficiency and identifying areas where automation yields the greatest benefits.
ERP systems offer far more advanced workflow automation than traditional methods. This stems from their integrated nature and ability to connect various business functions. Traditional methods, often reliant on disparate software and manual intervention, struggle to match the level of automation achievable with a comprehensive ERP solution. The impact of automation on efficiency and productivity is therefore significantly greater with ERP.
ERP Workflow Automation Capabilities
ERP systems excel at automating complex, multi-step processes. This automation reduces manual effort, minimizes errors, and ensures consistency. The impact on efficiency is substantial, freeing up employees to focus on higher-value tasks. Increased productivity is a direct consequence of reduced processing time and improved accuracy. Areas where automation is most beneficial include:
- Order processing: From order placement to fulfillment, ERP systems can automate tasks like inventory checks, order confirmation, shipping label generation, and invoice creation.
- Procurement: Automated purchase order generation, vendor communication, and invoice processing significantly streamline procurement workflows.
- Production planning: ERP systems can automate production scheduling, resource allocation, and materials management, optimizing production efficiency.
- Financial reporting: Automated financial reporting and data analysis provide real-time insights into the financial health of the business.
Traditional Business Management Workflow Automation
While traditional business management lacks the integrated automation capabilities of ERP, some automation is still possible. However, this often involves separate, often incompatible, software solutions or a combination of manual processes and limited automation tools. The impact on efficiency is less significant compared to ERP, and productivity gains are typically more modest. Areas where some automation might be achieved include:
- Spreadsheet automation: Using macros and formulas in spreadsheets can automate some repetitive tasks, such as data entry or report generation. However, this is often limited in scope and prone to errors if not carefully managed.
- Email automation: Automated email responses and notifications can improve communication efficiency, though integration with other systems is often lacking.
- Basic inventory management: Simple inventory tracking systems can automate some aspects of stock management, but these are typically less sophisticated than those integrated within an ERP system.
User Experience and Adoption
The success of any business management system, whether ERP or traditional, hinges significantly on its user experience and the rate of adoption among employees. A system that is difficult to use or understand will likely lead to low productivity, resistance to change, and ultimately, failure to achieve the intended benefits. This section compares the user experience and adoption challenges and strategies for both ERP and traditional business management approaches.
ERP systems, with their integrated modules and complex functionalities, often present a steeper learning curve compared to traditional, often siloed, methods. Traditional methods, however, may lack the streamlined workflow and integrated data that an ERP system provides, potentially leading to frustration from a user perspective in terms of efficiency and data access. The level of user experience and adoption is influenced by a multitude of factors, including system design, training, and ongoing support.
ERP System User Experience and Adoption Factors
ERP systems typically feature a centralized database and integrated modules, offering a potentially more streamlined workflow. However, the complexity of these systems, their extensive functionalities, and the often less intuitive interfaces can pose challenges. Successful ERP adoption requires comprehensive training programs, ongoing support, and a system designed with user-friendliness in mind. Companies like SAP have invested heavily in improving the user experience of their ERP systems, moving towards more intuitive interfaces and user-friendly dashboards. For example, SAP Fiori provides a simplified, role-based user interface that streamlines access to key functionalities. Failure to address these factors can lead to user resistance, low adoption rates, and ultimately, a poor return on investment.
Traditional Business Management System User Experience and Adoption Factors
Traditional business management systems, often comprised of disparate software applications and manual processes, can present their own set of user experience challenges. Data may be scattered across multiple systems, leading to inefficiencies and potential for errors. Workflows might be fragmented and lack the automation capabilities of an ERP system. User training might be less structured, and ongoing support could be less readily available. The lack of integration can create frustration, especially for employees who need to access information from multiple sources. However, the simplicity of individual applications, if well-designed, can lead to faster initial adoption compared to complex ERP systems. For example, a small business using separate accounting and inventory management software might find these easier to learn than a fully integrated ERP system.
Challenges in User Training and Support
Effective training and ongoing support are crucial for successful user adoption in both ERP and traditional systems. ERP systems, given their complexity, often require more extensive training programs, potentially involving multiple sessions and ongoing support channels. Traditional systems, while simpler in individual application, may still require training on multiple applications and processes. Challenges include time constraints for training, varying levels of technical expertise among users, and the need for ongoing support to address questions and resolve issues. Furthermore, maintaining up-to-date documentation and providing easy access to help resources is critical for both approaches. The lack of adequate training and support can lead to user frustration, errors, and ultimately, system failure.
Strategies for Improving User Experience and Adoption
Several strategies can improve user experience and adoption in both ERP and traditional business management systems. These include investing in user-friendly interfaces, providing comprehensive training programs tailored to different user roles, establishing clear communication channels for ongoing support, and gathering user feedback to make continuous improvements. For ERP systems, this might involve implementing a phased rollout, focusing on key modules first, and providing ongoing support and training throughout the implementation process. For traditional systems, this might involve streamlining workflows, integrating applications where possible, and providing clear, concise documentation. Regular system evaluations and user feedback sessions can identify areas for improvement and ensure that the system remains relevant and effective over time. The use of gamification techniques in training and the provision of readily accessible online help resources are further strategies to enhance user experience and adoption.
Security and Risk Management
The choice between an ERP system and traditional business management methods significantly impacts an organization’s security posture and risk profile. While both approaches present unique vulnerabilities, the inherent complexities and centralized nature of ERP systems necessitate a more robust and comprehensive security strategy. This section will compare the security features, potential threats, and mitigation strategies associated with each approach.
ERP systems, by consolidating data and processes, create a single point of vulnerability. A successful breach could compromise a vast amount of sensitive information. Conversely, traditional systems, often fragmented across various departments and applications, may present a more distributed risk profile, but lack the centralized control offered by an ERP.
ERP System Security Features, Vulnerabilities, and Mitigation Strategies
ERP systems typically incorporate robust security features, including access controls, encryption, audit trails, and regular security updates. However, their complexity can lead to vulnerabilities such as SQL injection attacks, cross-site scripting (XSS), and unauthorized access. Effective mitigation involves rigorous security testing, penetration testing, multi-factor authentication (MFA), and employee training on security best practices. Regular software updates are critical to patching known vulnerabilities. Implementing a robust security information and event management (SIEM) system can also aid in threat detection and response.
Traditional Business Management Security Features, Vulnerabilities, and Mitigation Strategies
Traditional business management methods often rely on a patchwork of individual systems and security measures. This decentralized approach can lead to inconsistencies in security practices and increased vulnerability. Common vulnerabilities include weak passwords, outdated software, and lack of centralized monitoring. Mitigation strategies involve standardizing security policies across all systems, implementing strong password policies, and using antivirus and firewall protection. Regular security audits and employee training are also essential. Data backups and disaster recovery planning are crucial to minimize the impact of potential breaches.
Comparison Table: ERP vs. Traditional Business Management Security
Feature | ERP System | Traditional Business Management | Mitigation Strategies |
---|---|---|---|
Security Features | Centralized access control, encryption, audit trails, integrated security modules | Decentralized security measures, varied levels of protection across different systems | Implement strong authentication, regular security audits, consistent security policies across all systems |
Vulnerabilities | Single point of failure, complex configuration, potential for system-wide breaches | Fragmented security, inconsistencies in protection, increased risk of individual system compromises | Regular security testing (penetration testing, vulnerability scanning), employee security awareness training, incident response plan |
Data Loss Prevention (DLP) | Integrated DLP tools, centralized monitoring and control | Dependent on individual system DLP capabilities, lack of unified monitoring | Implement consistent DLP policies across all systems, centralized monitoring of data access and usage |
Risk Management | Comprehensive risk assessment, integrated risk management tools | Fragmented risk assessment, inconsistent risk mitigation strategies | Develop a comprehensive risk management framework, regular risk assessments, proactive mitigation strategies |
Industry-Specific Applications
The choice between an ERP system and traditional business management approaches significantly depends on the specific industry and its unique operational requirements. Industries with complex, interconnected processes often find ERP systems invaluable, while others may thrive with more tailored, simpler solutions. Understanding these industry-specific nuances is crucial for making an informed decision.
ERP systems excel in environments demanding high levels of integration and data visibility across multiple departments. Conversely, traditional methods, often characterized by disparate systems and manual processes, can be sufficient for smaller businesses or those with less intricate operations. The following sections examine these differences across several key sectors.
ERP System Suitability: Manufacturing and Supply Chain Management
Manufacturing and supply chain management are industries where ERP systems demonstrably enhance efficiency and competitiveness. The intricate processes involved, from raw material procurement to finished goods delivery, demand seamless data flow and real-time visibility. ERP systems provide this by integrating planning, production, inventory management, and logistics into a single platform. This integrated approach allows for optimized production scheduling, reduced inventory costs, and improved delivery times. For example, a large automotive manufacturer using an ERP system can accurately predict demand, optimize production runs based on real-time inventory levels, and manage the complex supply chain involving thousands of parts and suppliers with greater precision than using disparate, unconnected systems. The benefits include reduced waste, improved on-time delivery, and enhanced overall profitability. Conversely, smaller manufacturers or those with simpler production processes might find the complexity and cost of implementing an ERP system outweigh the benefits. They might find traditional, less integrated methods sufficient for their needs.
Traditional Business Management Prevalence: Small-Scale Retail and Service Businesses
Many small-scale retail and service businesses continue to rely on traditional business management methods. These businesses often have simpler operational structures and fewer interconnected departments. The investment in a comprehensive ERP system may be unjustified given their scale and operational complexity. A small independent bookstore, for example, might manage inventory with a simple spreadsheet, track sales with a point-of-sale system, and handle customer relationships through a basic database. While these systems are not integrated, they suffice for their operational needs. Implementing an ERP system would introduce unnecessary complexity and cost without offering commensurate benefits. However, as these businesses grow, the limitations of traditional methods become apparent, potentially hindering scalability and efficient data management. The lack of integrated data can make strategic decision-making more difficult, and managing increasing complexity becomes challenging.
Impact on Industry Competitiveness
The choice between ERP and traditional business management significantly impacts industry competitiveness. In industries with complex operations and high levels of competition, adopting an ERP system often provides a crucial competitive advantage. The enhanced efficiency, improved data visibility, and streamlined processes enable businesses to respond more quickly to market changes, optimize resource allocation, and ultimately deliver superior products or services. Conversely, businesses that rely on outdated, fragmented systems may struggle to keep pace with competitors who leverage the power of integrated ERP solutions. For example, in the fast-paced consumer electronics industry, companies using ERP systems can efficiently manage product lifecycles, respond quickly to shifting consumer demands, and optimize their supply chains to stay ahead of the competition. Conversely, a company relying on disparate, unconnected systems may experience delays, inefficiencies, and ultimately lose market share.
FAQ Resource
ERP vs. Traditional Business Management: Which One Wins? – What are the common pitfalls of ERP implementation?
Common pitfalls include inadequate planning, insufficient user training, poor data migration, and a lack of executive sponsorship.
Can a small business benefit from an ERP system?
While larger businesses often benefit most, some smaller businesses with complex operations or rapid growth potential can also find ERP systems advantageous, though cloud-based solutions are generally more suitable.
How long does it typically take to implement an ERP system?
Implementation timelines vary greatly depending on the size and complexity of the business and the chosen ERP solution. It can range from several months to over a year.
What are the key considerations for choosing an ERP vendor?
Key considerations include vendor reputation, industry experience, software functionality, scalability, integration capabilities, and ongoing support services.