Best ERP Systems for Manufacturing Companies
Defining Manufacturing ERP Needs
Selecting the right Enterprise Resource Planning (ERP) system is crucial for manufacturing companies of all sizes. A well-implemented ERP system can streamline operations, improve efficiency, and boost profitability. Understanding the specific needs of your manufacturing business is the first step in finding the ideal solution. This involves identifying core functionalities, considering your business size, and defining key performance indicators (KPIs) for success.
Choosing the right ERP system requires a clear understanding of your business’s unique requirements. Different functionalities are prioritized depending on factors such as the size of the company, the complexity of the manufacturing process, and the overall business goals. Careful consideration of these aspects is vital to ensure a successful ERP implementation.
Core Functionalities of Manufacturing ERP Systems
Manufacturing ERP systems must offer a comprehensive suite of tools to manage all aspects of the production process. These systems should integrate various departments, providing a holistic view of the business. This integrated approach minimizes data silos and ensures efficient information flow.
- Production Planning and Scheduling: This functionality allows for efficient planning of production runs, considering factors such as material availability, machine capacity, and labor resources. It enables the creation of detailed production schedules and facilitates just-in-time (JIT) inventory management.
- Inventory Management: Effective inventory management is paramount in manufacturing. The ERP system should provide real-time visibility into inventory levels, track material usage, and manage warehouse operations. This ensures that the right materials are available at the right time, minimizing stockouts and reducing waste.
- Supply Chain Management: Integrating with suppliers and distributors is crucial. The ERP system should facilitate communication and collaboration throughout the supply chain, improving procurement processes and ensuring timely delivery of materials.
- Quality Control: Tracking and managing quality throughout the production process is vital. The ERP system should support quality control measures, enabling the identification and resolution of defects early in the process.
- Financial Management: Manufacturing ERP systems should integrate financial processes, providing real-time insights into costs, profitability, and overall financial health. This allows for better decision-making and improved financial control.
ERP Needs Across Different Manufacturing Business Sizes
The specific ERP needs vary significantly depending on the size of the manufacturing company. Small businesses have different priorities compared to large enterprises.
- Small Manufacturing Businesses: Often prioritize affordability and ease of use. They may require simpler systems with basic functionalities focused on inventory management, production scheduling, and financial accounting. A cloud-based solution might be preferred due to its lower upfront cost and scalability.
- Medium-Sized Manufacturing Businesses: Require more sophisticated functionalities, including advanced planning and scheduling, supply chain management, and quality control. Integration with other business systems is often a key requirement. They may need a system that can handle greater complexity and data volume than a small business.
- Large Manufacturing Businesses: Demand highly scalable and customizable ERP systems capable of handling massive data volumes and complex manufacturing processes. Integration with various enterprise systems is essential, along with advanced analytics and reporting capabilities. These businesses may also require robust security features to protect sensitive data.
Key Performance Indicators (KPIs) for Manufacturing ERP Systems
Effective monitoring of key performance indicators is essential to assess the success of an ERP implementation and identify areas for improvement. Manufacturing ERP systems should track and report on a variety of KPIs to provide valuable insights into operational efficiency and profitability.
- On-Time Delivery Rate: Measures the percentage of orders delivered on or before the scheduled delivery date. A high on-time delivery rate indicates efficient production and supply chain management.
- Production Efficiency: Measures the ratio of output to input resources, indicating how effectively resources are utilized in the production process. Improvements in production efficiency often translate to cost savings.
- Inventory Turnover Rate: Measures how quickly inventory is sold or used, indicating the efficiency of inventory management. A high inventory turnover rate suggests effective inventory control and minimizes storage costs.
- Total Manufacturing Cost: Tracks the overall cost of production, including direct and indirect costs. Analyzing this KPI helps identify areas for cost reduction and improve profitability.
- Defect Rate: Measures the percentage of defective products produced, indicating the effectiveness of quality control measures. A low defect rate translates to higher customer satisfaction and reduced waste.
Top ERP Vendors for Manufacturing: Best ERP Systems For Manufacturing Companies
Selecting the right Enterprise Resource Planning (ERP) system is crucial for manufacturing companies seeking to optimize their operations and gain a competitive edge. The market offers a wide array of solutions, each with its own strengths and weaknesses. This section focuses on five leading ERP vendors specializing in manufacturing, comparing their offerings to help manufacturers make informed decisions.
Best ERP Systems for Manufacturing Companies – Choosing the right ERP system is a significant investment, requiring careful consideration of various factors including company size, specific manufacturing processes, budget, and future scalability needs. A thorough understanding of each vendor’s capabilities is essential for a successful implementation.
Leading ERP Vendors and Their Strengths and Weaknesses
The following table compares five leading ERP vendors known for their robust manufacturing solutions. It’s important to note that the strengths and weaknesses can vary depending on specific industry segments and individual company requirements.
Vendor | Strengths | Weaknesses | Example Successful Implementation |
---|---|---|---|
SAP | Highly scalable, comprehensive functionality, strong industry expertise, global reach. | Can be complex to implement and expensive, requires significant IT resources. | Many Fortune 500 manufacturing companies utilize SAP, including companies in the automotive and aerospace industries, though specific examples are often kept confidential due to competitive reasons. |
Oracle | Robust functionality, strong in supply chain management, good integration capabilities. | Can be expensive and complex to implement, requires specialized expertise. | Many large multinational manufacturers use Oracle, including those in the food and beverage and high-tech sectors, but specific examples often remain undisclosed for competitive reasons. |
Microsoft Dynamics 365 | User-friendly interface, relatively easy to implement, good value for smaller to medium-sized businesses. | May lack some of the advanced features of larger ERP systems, scalability might be a concern for rapid growth. | Numerous mid-sized manufacturing companies successfully utilize Microsoft Dynamics 365 for improved efficiency and streamlined operations. Specific examples are often protected for business reasons. |
Infor | Industry-specific solutions, strong focus on manufacturing processes, good integration with other business systems. | May not be as widely known as some of the larger vendors, support might be more localized depending on the specific solution. | Infor serves various manufacturing segments with tailored solutions, but specific client examples are generally confidential. |
Epicor | Strong focus on mid-market manufacturing, user-friendly interface, good value for the features offered. | Scalability might be a limitation for very large enterprises, integration with certain legacy systems could pose challenges. | Many mid-sized and smaller manufacturing companies successfully leverage Epicor for improved production planning and inventory management, though case studies are often limited in public detail for competitive reasons. |
Cost and Return on Investment (ROI)
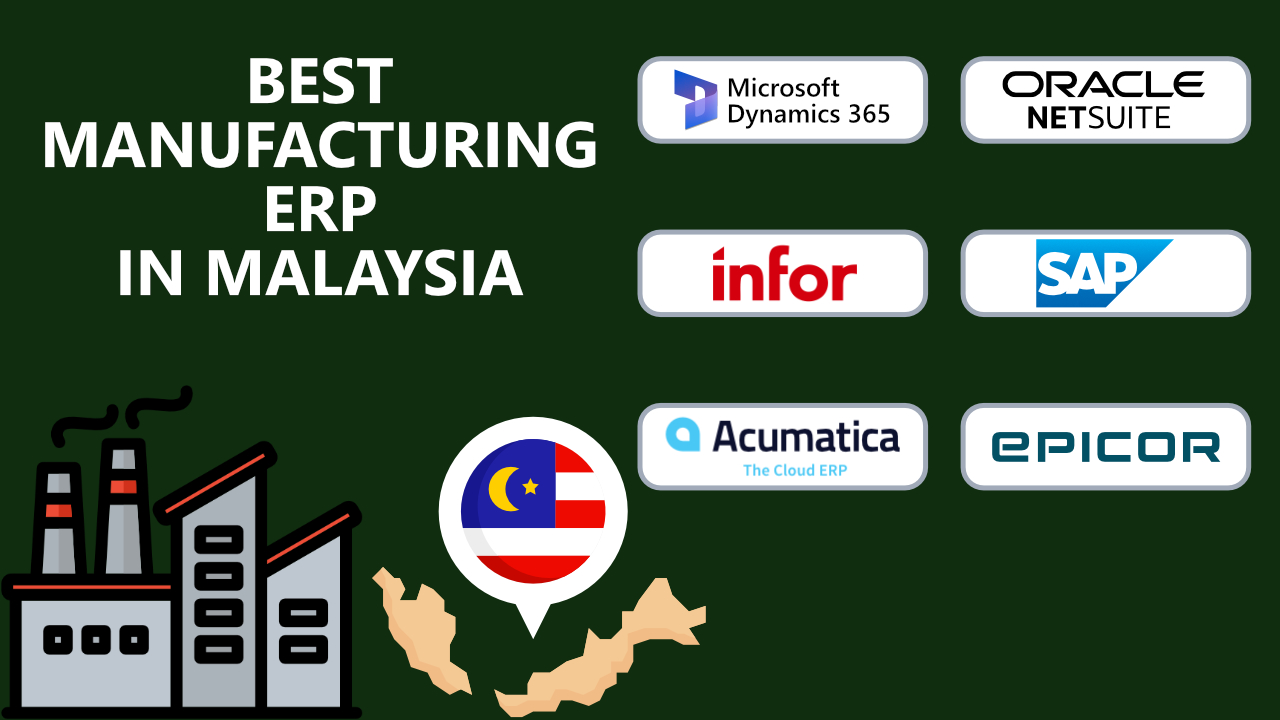
Implementing a manufacturing ERP system represents a significant investment, demanding careful consideration of both upfront costs and long-term returns. Understanding the various cost components and developing a robust ROI calculation is crucial for justifying the expenditure and ensuring successful project outcomes. This section details the typical costs involved and explores methods for evaluating the financial benefits of ERP implementation.
Typical Costs Associated with Manufacturing ERP Systems
The total cost of ownership (TCO) for a manufacturing ERP system encompasses various elements, extending beyond the initial software license fee. A comprehensive budget should account for all these factors to accurately assess the financial commitment.
- Software License Fees: This is the cost of purchasing the ERP software itself, often varying based on the number of users, modules implemented, and the vendor’s pricing structure. Larger enterprises typically pay more for broader functionality and more users.
- Implementation Costs: This significant portion of the TCO includes consulting fees for project management, system configuration, data migration, and user training. The complexity of the implementation, the size of the organization, and the chosen vendor influence these costs considerably. Expect significant time commitment from internal staff as well.
- Hardware and Infrastructure: Depending on the chosen deployment model (cloud-based or on-premise), costs may include server hardware, network upgrades, and database management systems. Cloud solutions often shift these costs to a subscription model, reducing upfront capital expenditure but increasing recurring operational expenses.
- Data Migration Costs: Transferring existing data from legacy systems to the new ERP system requires careful planning and execution. The cost depends on the volume and complexity of the data, and any necessary data cleansing or transformation processes.
- Integration Costs: Integrating the ERP system with existing systems (e.g., CRM, supply chain management software) adds complexity and cost. Custom integrations often require specialized expertise and development.
- Ongoing Maintenance and Support: Post-implementation, ongoing costs include software maintenance, technical support, and potentially user training refreshers. Vendors typically offer various support packages at different price points.
Methods for Calculating ROI of ERP System Implementation
Calculating the ROI of an ERP implementation requires a clear understanding of both the costs (as detailed above) and the anticipated benefits. Several approaches can be used to quantify these benefits and calculate the return on investment.
- Cost Savings: Identify areas where the ERP system will reduce costs, such as streamlined processes, reduced inventory, improved efficiency, and lower labor costs. Quantify these savings with specific examples and realistic projections.
- Revenue Increases: Determine how the ERP system will improve revenue generation, such as better forecasting, improved customer service, and faster order fulfillment. These increases should be backed by market analysis and sales projections.
- Improved Efficiency Metrics: Track key performance indicators (KPIs) before and after implementation to measure improvements in areas like production cycle time, order fulfillment time, and inventory turnover. These metrics should be carefully chosen and tracked consistently.
- Return on Investment Formula: A common formula for calculating ROI is:
ROI = (Net Benefits – Total Costs) / Total Costs
This formula expresses the ROI as a percentage.
Examples of Positive ROI from ERP Investments
Many manufacturing companies have demonstrated significant ROI from their ERP investments. While specific figures are often confidential, case studies frequently highlight improved operational efficiency, reduced costs, and increased revenue. For instance, a mid-sized manufacturer might see a 15% reduction in inventory costs and a 10% increase in production efficiency within the first year post-implementation, leading to a substantial positive ROI. Another example could be a company experiencing a 20% reduction in order fulfillment time, leading to increased customer satisfaction and repeat business. These are illustrative examples; the actual ROI varies significantly depending on the company’s size, industry, and specific implementation details.
Industry-Specific Considerations
Choosing the right ERP system is crucial for manufacturing companies, and this decision becomes even more critical when considering the unique demands of various industries. Different sectors have distinct operational processes, regulatory requirements, and production complexities that necessitate specialized ERP functionalities. Understanding these industry-specific needs is vital for selecting a system that delivers optimal efficiency and ROI.
ERP System Features for the Food and Beverage Industry
The food and beverage industry faces stringent regulations regarding safety, traceability, and quality control. ERP systems tailored for this sector must incorporate features that ensure compliance and optimize production processes within these constraints.
- Traceability and Recall Management: Robust tracking capabilities are essential for identifying the source of potential contamination or quality issues, enabling swift and efficient product recalls. This includes detailed lot tracking, expiration date management, and integration with supply chain partners for complete visibility.
- Quality Control and Assurance: Features for managing quality control processes, including testing results, inspections, and certifications, are vital. The system should facilitate adherence to standards like HACCP (Hazard Analysis and Critical Control Points) and GMP (Good Manufacturing Practices).
- Regulatory Compliance: The ERP system should help maintain compliance with various food safety regulations, such as FDA (Food and Drug Administration) requirements in the US or equivalent regulations in other countries. This includes features for managing labeling, ingredient declarations, and allergen information.
- Inventory Management for Perishable Goods: Efficient management of perishable goods is crucial. The system needs to incorporate features for managing shelf life, FIFO (First-In, First-Out) inventory control, and real-time inventory visibility to minimize waste.
ERP System Features for the Automotive Industry
The automotive industry demands high precision, complex supply chains, and robust quality control. ERP systems need to handle the intricacies of manufacturing vehicles and their components effectively.
- Bill of Materials (BOM) Management: Precise and detailed BOM management is crucial, considering the complex assembly processes involved in vehicle manufacturing. The system should allow for efficient management of variations and revisions in BOMs across different vehicle models.
- Supply Chain Management: Effective management of a vast and complex supply chain is vital. The ERP system should provide tools for coordinating with numerous suppliers, managing logistics, and tracking components throughout the entire supply chain.
- Quality Control and Lean Manufacturing: Implementing lean manufacturing principles is critical for efficiency. The ERP system should facilitate this by providing tools for tracking production metrics, identifying bottlenecks, and optimizing processes for continuous improvement.
- Production Scheduling and Capacity Planning: Precise scheduling and capacity planning are essential for meeting production targets and optimizing resource utilization in the highly complex automotive manufacturing process.
ERP System Features for the Pharmaceutical Industry
The pharmaceutical industry operates under the strictest regulatory oversight, demanding impeccable quality control, traceability, and compliance.
- Batch Tracking and Serialization: Comprehensive batch tracking and serialization are crucial for ensuring product traceability and complying with regulations such as the Drug Supply Chain Security Act (DSCSA) in the US. This involves unique identification and tracking of each individual unit of medication throughout its lifecycle.
- Good Manufacturing Practices (GMP) Compliance: The ERP system must support complete compliance with GMP guidelines, including documentation management, audit trails, and controlled access to critical data. This ensures adherence to the highest quality and safety standards.
- Quality Management System (QMS) Integration: Seamless integration with a QMS is essential for managing quality control processes, non-conformances, and corrective actions. This ensures continuous improvement and maintains compliance with regulatory requirements.
- Regulatory Compliance and Reporting: The system should simplify the generation of reports required by regulatory agencies, such as the FDA, to streamline compliance efforts and minimize potential risks.
Security and Data Management
Manufacturing ERP systems house incredibly sensitive data, encompassing everything from financial records and production schedules to intellectual property and customer information. Robust security measures are paramount not only for regulatory compliance but also for safeguarding a company’s competitive advantage and preventing costly disruptions. A breach can lead to significant financial losses, reputational damage, and legal repercussions.
Data security in a manufacturing ERP system is multifaceted, requiring a layered approach encompassing physical, network, and application security. This includes protecting data both in transit and at rest, utilizing encryption, access controls, and regular security audits. The importance of data integrity is equally crucial, ensuring data accuracy and reliability throughout the entire manufacturing process. Effective data management practices are essential for maintaining operational efficiency and facilitating informed decision-making.
Security Features Offered by Leading ERP Vendors
Leading ERP vendors understand the critical need for robust security and incorporate a range of features designed to protect sensitive manufacturing data. These features typically include encryption of data both in transit (using protocols like HTTPS) and at rest (using database encryption), multi-factor authentication (MFA) to restrict access to authorized personnel only, and role-based access control (RBAC) to limit user permissions based on their job function. Regular security updates and patching are also crucial to address vulnerabilities and prevent exploits. Many vendors also offer features such as intrusion detection and prevention systems, data loss prevention (DLP) tools, and audit trails to monitor system activity and identify potential security breaches. For example, SAP offers a comprehensive security suite integrated into its S/4HANA manufacturing solution, while Oracle NetSuite provides robust security features tailored to the needs of various manufacturing sectors. These features often include advanced analytics capabilities to detect anomalies and potential threats in real-time.
Best Practices for Managing and Protecting Data within a Manufacturing ERP System
Effective data management and protection within a manufacturing ERP system requires a proactive and multi-layered approach. This begins with establishing clear data governance policies and procedures, defining roles and responsibilities for data security, and implementing strong access control mechanisms. Regular security awareness training for employees is vital to educate them about potential threats and best practices for protecting sensitive information. Implementing a robust backup and recovery strategy is crucial to ensure business continuity in the event of a data loss or system failure. This includes regular backups stored offsite in a secure location, and a well-tested disaster recovery plan. Regular security audits and penetration testing should be conducted to identify vulnerabilities and ensure the effectiveness of security controls. Finally, staying current with the latest security best practices and industry standards is essential to mitigate emerging threats. For instance, adhering to standards like ISO 27001 demonstrates a commitment to data security and can build trust with customers and partners.
Scalability and Future-Proofing
Choosing an ERP system is a significant investment, and it’s crucial to select a solution that can adapt to your company’s evolving needs. A scalable ERP system allows for growth without requiring a complete system overhaul, saving time, money, and resources in the long run. Future-proofing your ERP choice ensures your system remains relevant and efficient as your manufacturing processes and technologies advance.
The long-term viability of an ERP system hinges on its ability to handle increasing data volumes, accommodate new functionalities, and integrate with emerging technologies. Assessing this involves examining the system’s architecture, its capacity for customization and expansion, and the vendor’s commitment to ongoing development and support. A system with a robust API (Application Programming Interface) and open architecture will be easier to integrate with other systems and adapt to future needs. Consider the vendor’s track record of updates and their roadmap for future features. Companies with a history of successful system upgrades and a clear vision for future development are more likely to offer a future-proof solution.
ERP System Scalability Assessment Checklist, Best ERP Systems for Manufacturing Companies
Evaluating the scalability of an ERP system requires a thorough assessment. This checklist provides a structured approach to identifying key factors that contribute to a system’s ability to grow with your business.
- System Architecture: Determine if the system uses a modular or monolithic architecture. Modular systems offer greater scalability as they allow for adding or upgrading individual modules as needed, without affecting the entire system.
- Database Capacity: Assess the database’s capacity to handle increasing data volumes. Consider the projected growth of your data and ensure the system can accommodate this growth without performance degradation. For example, a company expecting a 50% increase in production data within the next three years should verify the database can handle this volume.
- User Capacity: Evaluate the system’s ability to support an increasing number of users. This includes considering both concurrent users and overall user growth projections. A company planning significant workforce expansion needs an ERP system capable of supporting a larger user base.
- Integration Capabilities: Examine the system’s API and its ability to integrate with other systems, such as CRM, supply chain management, and other specialized applications. Seamless integration is crucial for scalability and efficient data flow.
- Vendor Support and Updates: Evaluate the vendor’s track record of providing timely updates, patches, and support. Regular updates ensure the system remains secure, compatible with new technologies, and optimized for performance. Look for a vendor with a strong commitment to long-term support and a clear roadmap for future development. For instance, a vendor’s commitment to cloud-based infrastructure and regular software updates ensures long-term compatibility and security.
- Customization Options: Assess the system’s ability to be customized to meet specific business requirements. A highly customizable system can adapt more easily to evolving needs, avoiding costly system replacements in the future. For example, a manufacturing company specializing in custom-made products would benefit from a highly customizable ERP system to manage unique product configurations and processes.
Long-Term Viability and Future-Proofing Strategies
Choosing a future-proof ERP system involves considering several factors beyond immediate needs. This includes anticipating technological advancements and ensuring the system can adapt to them.
A future-proof ERP system is not just about the technology itself, but also about the vendor’s commitment to ongoing innovation and support.
Adopting a cloud-based ERP solution can enhance future-proofing capabilities. Cloud-based systems typically offer automatic updates, improved scalability, and enhanced accessibility. Furthermore, consider the vendor’s commitment to emerging technologies such as AI and machine learning. Integration with these technologies can significantly enhance efficiency and decision-making capabilities in the long term. For example, a manufacturing company could integrate AI-powered predictive maintenance tools into their ERP system to optimize equipment maintenance schedules and minimize downtime.
User Experience and Training
Implementing a new ERP system is a significant undertaking for any manufacturing company. The success of this implementation hinges not only on the system’s functionality but also on its user-friendliness and the effectiveness of the training provided. A poorly designed interface or inadequate training can lead to low user adoption, decreased productivity, and ultimately, a failed ERP implementation. Therefore, careful consideration of user experience and comprehensive training programs are crucial for maximizing the return on investment.
A user-friendly interface is paramount for efficient and accurate data entry and retrieval within a manufacturing ERP system. Intuitive navigation, clear visual cues, and readily accessible information significantly reduce the learning curve and minimize errors. Features like customizable dashboards, role-based access controls, and integrated help systems can dramatically improve user experience, fostering a more positive attitude towards the new system and encouraging greater engagement. A well-designed interface reduces frustration, increases user confidence, and promotes accurate data input, all of which are essential for the success of a manufacturing ERP system.
Interface Design and Usability
Effective interface design considers the specific needs and skill levels of the manufacturing workforce. Clear, concise labels, logical data organization, and consistent visual elements minimize confusion and improve efficiency. The system should be easily navigable, with intuitive workflows that mirror existing processes where possible. Features such as drag-and-drop functionality, customizable dashboards, and integrated reporting tools can enhance usability and improve overall productivity. For example, a system that allows production managers to quickly access real-time production data through an easily navigable dashboard will significantly improve their ability to make informed decisions and respond effectively to unexpected issues. The use of consistent color-coding, clear icons, and readily accessible help files further enhances the user experience and facilitates efficient operation.
Training and Support Options
ERP vendors typically offer a range of training and support options to ensure successful user adoption. These options often include instructor-led training, online tutorials, self-paced learning modules, and ongoing technical support. Instructor-led training provides hands-on experience and allows users to ask questions and receive personalized guidance. Online tutorials and self-paced learning modules offer flexibility and allow users to learn at their own pace. Technical support provides assistance with troubleshooting and problem-solving. The specific training and support options offered will vary depending on the vendor and the chosen ERP system. For example, some vendors might offer comprehensive training programs that include classroom instruction, online modules, and on-site support, while others may offer more limited training options.
Best Practices for User Adoption
Successful user adoption requires a multi-faceted approach that addresses both technical and human factors. This includes thorough needs assessment, comprehensive training, ongoing support, and active user engagement. A well-planned change management strategy is critical, involving all stakeholders from the beginning. This strategy should clearly communicate the benefits of the new system, address concerns, and provide opportunities for feedback. Regular feedback sessions, user surveys, and ongoing system improvements are essential for maintaining user satisfaction and maximizing the long-term value of the ERP system. Furthermore, assigning dedicated super-users within each department can provide crucial on-the-ground support and mentorship, accelerating the adoption process and fostering a culture of collaboration and problem-solving. By fostering a positive and supportive environment, companies can significantly increase the likelihood of successful user adoption and realize the full potential of their ERP investment.
Case Studies of Successful ERP Implementations
The successful implementation of an ERP system can significantly transform a manufacturing company’s operations, leading to improved efficiency, reduced costs, and enhanced profitability. Examining real-world examples provides valuable insights into the challenges and rewards associated with such undertakings. The following case studies highlight the strategies employed by various manufacturing firms to achieve successful ERP implementations and the tangible benefits they reaped.
Successful ERP Implementation at Acme Manufacturing
Acme Manufacturing, a mid-sized producer of automotive parts, faced challenges with inventory management, production scheduling, and communication between different departments. Their legacy system was outdated and lacked the integration necessary for efficient operations. After a thorough evaluation, Acme chose to implement a cloud-based ERP system from a leading vendor. The implementation process involved several key steps: a comprehensive needs assessment, careful data migration, extensive employee training, and phased rollout. Initially, Acme encountered resistance from some employees accustomed to the old system. However, the company addressed this by providing thorough training and emphasizing the long-term benefits of the new system. The challenges related to data migration were overcome through careful planning and data cleansing. Post-implementation, Acme saw a 15% reduction in inventory costs, a 10% increase in production efficiency, and a significant improvement in order fulfillment times. Their improved visibility into real-time data enabled better decision-making and proactive problem-solving.
Improved Efficiency at Beta Precision Components
Beta Precision Components, a manufacturer of high-precision instruments, implemented an ERP system to improve their supply chain management. Prior to implementation, Beta struggled with inaccurate forecasting, leading to stockouts and excess inventory. The new ERP system provided advanced forecasting capabilities, enabling them to optimize inventory levels and reduce waste. The implementation itself was a complex undertaking, requiring extensive customization to meet Beta’s specific needs. The company overcame the challenges of customization by working closely with the ERP vendor and establishing a dedicated implementation team. The team also prioritized thorough testing at each stage to ensure the system functioned as intended. Following the successful implementation, Beta witnessed a 20% reduction in inventory holding costs and a 12% improvement in on-time delivery performance. Improved supply chain visibility also enabled them to negotiate better terms with suppliers.
Streamlined Operations at Gamma Electronics
Gamma Electronics, a large electronics manufacturer, implemented an ERP system to improve collaboration and communication across its global operations. Gamma’s previous system was fragmented, making it difficult to share information and track progress across different departments and geographical locations. The new ERP system provided a centralized platform for data management, enabling better collaboration and improved decision-making. A key challenge for Gamma was integrating the new ERP system with its existing legacy systems. This was accomplished through a phased approach, prioritizing the integration of critical systems first. Gamma also invested heavily in employee training to ensure a smooth transition and widespread adoption. The successful implementation resulted in a 10% reduction in operational costs, a 15% improvement in customer satisfaction, and enhanced visibility into global operations. The improved communication and collaboration also facilitated quicker responses to market changes and customer demands.
Essential FAQs
What is the average implementation time for a manufacturing ERP system?
Implementation timelines vary greatly depending on the size and complexity of the company and the chosen system, ranging from several months to over a year.
How can I ensure data security with my chosen ERP system?
Prioritize vendors offering robust security features like encryption, access controls, regular backups, and compliance with industry standards (e.g., ISO 27001).
What are the common challenges in ERP system integration?
Challenges include data migration issues, compatibility problems with legacy systems, and the need for extensive testing and validation.
What is the role of change management in a successful ERP implementation?
Effective change management involves thorough employee training, communication, and addressing concerns to ensure smooth user adoption and minimize disruption.