Why Every Business Needs ERP Software in 2025
The Evolving Business Landscape in 2025
The business world in 2025 is characterized by rapid technological advancement, increased global interconnectedness, and a growing reliance on data-driven decision-making. Businesses that fail to adapt to these changes risk falling behind competitors who leverage technology and data effectively. This section will explore these key trends and demonstrate how they highlight the crucial role of ERP software in maintaining a competitive edge.
Technological Advancements Impacting Businesses in 2025
Several key technological advancements are significantly shaping the business landscape in 2025. Artificial intelligence (AI) and machine learning (ML) are automating tasks, improving efficiency, and providing valuable insights from large datasets. The Internet of Things (IoT) connects devices and systems, generating vast amounts of data that can be used to optimize operations and improve decision-making. Cloud computing provides scalable and cost-effective solutions for data storage, processing, and application delivery. Blockchain technology offers secure and transparent solutions for supply chain management and data security. The convergence of these technologies creates a complex but highly efficient operational environment, demanding integrated systems for effective management. For example, a manufacturing company might use AI to predict equipment failures, IoT sensors to monitor production in real-time, and cloud computing to store and analyze the resulting data, all integrated through an ERP system.
The Increasing Importance of Data-Driven Decision-Making
Data is the new currency in the modern business world. In 2025, the ability to collect, analyze, and interpret data effectively is crucial for making informed decisions and gaining a competitive advantage. Businesses are increasingly relying on data analytics to understand customer behavior, optimize operations, and identify new opportunities. This data-driven approach requires robust systems capable of handling large volumes of data from diverse sources and providing actionable insights. ERP systems play a critical role in this process by consolidating data from various departments and providing a centralized platform for analysis. For instance, a retail company can use ERP data to analyze sales trends, predict future demand, and optimize inventory levels, leading to increased profitability and reduced waste.
Globalization and Interconnectedness Affecting Business Operations
Globalization and interconnectedness are transforming business operations in profound ways. Businesses are increasingly operating in global markets, interacting with suppliers, customers, and partners across geographical boundaries. This interconnectedness necessitates efficient and streamlined communication and collaboration across departments and locations. ERP systems facilitate this by providing a centralized platform for managing global operations, ensuring consistency in processes, and improving communication across different time zones and cultures. Consider a multinational corporation with operations in multiple countries. An ERP system allows them to manage inventory, track sales, and monitor financial performance across all locations from a single platform, fostering better coordination and control.
Comparison of Traditional and Modern ERP-Integrated Approaches
Aspect | Traditional Business Methods | Modern ERP-Integrated Approach |
---|---|---|
Data Management | Data siloed across departments, leading to inconsistencies and difficulties in analysis. | Centralized data repository, providing a single source of truth for improved decision-making. |
Process Efficiency | Manual processes, prone to errors and delays. | Automated workflows and streamlined processes, leading to increased efficiency and reduced costs. |
Supply Chain Management | Limited visibility into the supply chain, leading to potential disruptions. | Real-time visibility into the entire supply chain, enabling proactive management and improved responsiveness. |
Decision-Making | Decisions based on limited and potentially outdated information. | Data-driven decision-making based on real-time insights and comprehensive analysis. |
Core ERP Functionality and its Business Benefits
Enterprise Resource Planning (ERP) software offers a centralized system for managing and integrating all facets of a business. By connecting various departments and functions, ERP streamlines operations, improves efficiency, and provides valuable insights for better decision-making. This integrated approach contrasts sharply with disparate, siloed systems that often lead to data inconsistencies and operational bottlenecks.
ERP systems achieve this streamlining through a combination of integrated modules that manage different business functions. These modules work together seamlessly, eliminating the need for manual data entry and reconciliation between different systems. This automation reduces errors, saves time, and frees up employees to focus on higher-value tasks.
Streamlined Business Processes
ERP systems significantly enhance operational efficiency by automating repetitive tasks and improving data flow between departments. For instance, an order placed through the sales module automatically updates inventory levels in the inventory management module, triggering the procurement module to initiate the ordering of new stock if necessary. This automated process eliminates manual data entry, reduces the risk of errors, and ensures that all departments have access to the same, up-to-date information. This contrasts with traditional methods where manual data transfer between departments was common, leading to delays, inconsistencies, and potential errors.
Improved Efficiency Examples
Consider a manufacturing company using an ERP system. Before ERP implementation, tracking materials, managing production schedules, and coordinating shipping could be a complex, time-consuming process. With ERP, the company can efficiently manage its supply chain, track production in real-time, and optimize inventory levels, reducing lead times and minimizing waste. Similarly, a retail business can leverage ERP to improve customer service by providing real-time inventory visibility, enabling sales staff to accurately answer customer queries about product availability. The automation of tasks such as order processing and invoicing further frees up staff to focus on sales and customer relationships.
Integrated Financial Management
ERP systems offer comprehensive financial management capabilities, integrating accounting, budgeting, and financial reporting functions. This integration ensures accurate and timely financial data, enabling better financial planning and control. For example, an ERP system can automatically generate financial reports, track accounts receivable and payable, and manage the budgeting process, providing real-time insights into the company’s financial performance. This level of integration eliminates manual reconciliation of data from different systems, reducing the risk of errors and improving the accuracy of financial reporting. This contrasts with systems where finance data resides in isolated spreadsheets and databases, making accurate and timely financial reporting difficult and error-prone.
Real-time Data Visibility and Decision-Making
One of the most significant benefits of ERP is the real-time visibility it provides into all aspects of the business. This real-time data empowers managers to make informed decisions based on accurate, up-to-date information. For example, a company can use real-time sales data to adjust production schedules, optimize inventory levels, and anticipate future demand. Similarly, real-time financial data allows for proactive adjustments to budgets and spending plans. This data-driven approach to decision-making enables companies to respond quickly to changing market conditions and improve their overall performance. In contrast, reliance on outdated or incomplete data often leads to delayed responses and poor decision-making.
Addressing Specific Business Needs with ERP
ERP systems are not simply software packages; they are transformative tools capable of addressing a wide range of specific business needs. By integrating various departments and functions, ERP streamlines operations, improves efficiency, and ultimately drives profitability. This section will explore how ERP systems directly support crucial business areas, illustrating their tangible benefits.
ERP Support for Supply Chain Management and Optimization
Effective supply chain management is paramount for any business aiming for competitiveness and resilience. ERP systems provide the backbone for this, offering real-time visibility into the entire supply chain, from procurement to delivery. This visibility allows for proactive management of inventory levels, accurate demand forecasting, and efficient resource allocation. For example, an ERP system can automatically trigger a purchase order when inventory levels fall below a predefined threshold, preventing stockouts and ensuring continuous production. Furthermore, sophisticated ERP systems can leverage predictive analytics to anticipate future demand fluctuations, enabling businesses to optimize production schedules and avoid costly overstocking or understocking. This leads to reduced lead times, minimized storage costs, and improved customer satisfaction.
ERP Enhancement of Customer Relationship Management (CRM)
While often considered separate entities, ERP and CRM systems are highly synergistic. An integrated ERP and CRM system provides a unified view of customer interactions and transactions, empowering businesses to personalize their service and improve customer retention. For example, sales teams can access real-time information on customer order history, payment status, and support interactions, enabling them to provide more informed and proactive customer service. Marketing teams can leverage customer data to create targeted campaigns, improving marketing ROI. By integrating CRM with ERP’s inventory management capabilities, businesses can accurately predict customer demand and ensure timely delivery, further enhancing customer satisfaction. This seamless integration fosters stronger customer relationships, leading to increased loyalty and revenue.
Scenario: ERP Improves Inventory Control and Reduces Waste, Why Every Business Needs ERP Software in 2025
Imagine a manufacturing company producing specialized components. Without an ERP system, this company might experience inconsistencies in inventory tracking, leading to overstocking of slow-moving items and stockouts of critical components. This results in increased warehousing costs, potential production delays, and lost sales opportunities. However, by implementing an ERP system, the company gains real-time visibility into inventory levels, enabling them to optimize production based on actual demand. The ERP system can automatically generate alerts for low-stock items, triggering timely replenishment orders. Furthermore, it can track component usage, identifying potential waste or inefficiencies in the production process. By analyzing this data, the company can make informed decisions to improve production processes, reduce waste, and optimize resource allocation. This results in significant cost savings and improved profitability.
Comparison of Cloud-Based ERP vs. On-Premise Solutions
The choice between cloud-based and on-premise ERP solutions depends on various factors, including budget, IT infrastructure, and business needs. Cloud-based ERP offers scalability, accessibility, and reduced upfront costs, as businesses pay a subscription fee rather than investing in significant hardware and software infrastructure. On-premise solutions, however, offer greater control over data security and customization options. A company with stringent data security requirements or highly specific business processes might prefer an on-premise solution, despite the higher initial investment. Conversely, a rapidly growing company with limited IT resources might find a cloud-based solution more suitable due to its scalability and ease of implementation. The decision ultimately hinges on a careful assessment of the organization’s specific requirements and long-term goals.
Overcoming the Challenges of ERP Implementation
Implementing an Enterprise Resource Planning (ERP) system is a significant undertaking, often fraught with potential pitfalls. Success hinges not only on selecting the right software but also on meticulous planning, effective change management, and comprehensive user support. Failing to address these crucial aspects can lead to project delays, budget overruns, and ultimately, failure to realize the anticipated benefits of the ERP system.
Potential hurdles in ERP implementation are numerous and varied, ranging from inadequate planning and unrealistic expectations to resistance to change and insufficient user training. Successfully navigating these challenges requires a proactive and strategic approach, focusing on meticulous preparation, clear communication, and ongoing support throughout the entire implementation lifecycle.
Potential Hurdles and Mitigation Strategies
Several key challenges frequently arise during ERP implementations. These include data migration issues, integration complexities with existing systems, insufficient user training, lack of executive sponsorship, and inadequate change management processes. To mitigate these risks, organizations should conduct thorough due diligence during the selection process, establish clear project timelines and milestones, and ensure adequate resources are allocated. Robust data cleansing and validation procedures are crucial before migration, while phased implementation can minimize disruption. Addressing integration complexities requires careful planning and potentially the engagement of specialist consultants. Finally, securing strong executive sponsorship ensures buy-in and commitment from the top, crucial for overcoming resistance to change.
The Importance of Proper Planning and Change Management
Effective planning is the cornerstone of a successful ERP implementation. This involves defining clear objectives, identifying key stakeholders, and establishing realistic timelines and budgets. A detailed project plan should Artikel all phases of the implementation, including data migration, system configuration, testing, and training. Equally crucial is change management, which encompasses strategies to address the impact of the new system on employees, processes, and organizational culture. This might involve communication campaigns, training programs, and the establishment of support mechanisms to help employees adapt to the new system. For example, a company implementing a new ERP system might hold regular meetings to communicate progress, address concerns, and solicit feedback from employees. This proactive approach fosters buy-in and reduces resistance.
The Role of User Training and Ongoing Support
User training is paramount for successful ERP adoption. Employees need sufficient training to understand and utilize the new system effectively. This should involve both classroom-based training and hands-on experience with the system. Ongoing support is equally important, providing users with readily available assistance to address any issues or queries they may encounter. This might involve help desks, online tutorials, or dedicated support staff. For instance, a company could provide access to online training modules, FAQs, and a dedicated support team to answer questions and resolve issues promptly. This ensures that users feel comfortable using the system and are able to maximize its benefits.
A Step-by-Step Guide for Successful ERP Implementation
A successful ERP implementation follows a structured approach. This involves several key stages:
- Needs Assessment and Planning: Define business requirements, select appropriate ERP software, and develop a detailed project plan.
- System Selection and Customization: Choose the ERP system that best fits the organization’s needs and customize it accordingly.
- Data Migration and Integration: Cleanse and validate data, and integrate the ERP system with existing systems.
- Testing and Quality Assurance: Conduct thorough testing to identify and resolve any issues before go-live.
- Training and User Adoption: Provide comprehensive user training and support to ensure smooth adoption.
- Go-Live and Post-Implementation Support: Launch the ERP system and provide ongoing support to users.
- Continuous Improvement and Optimization: Regularly review and optimize the ERP system to ensure it continues to meet business needs.
The Role of Data Analytics in ERP
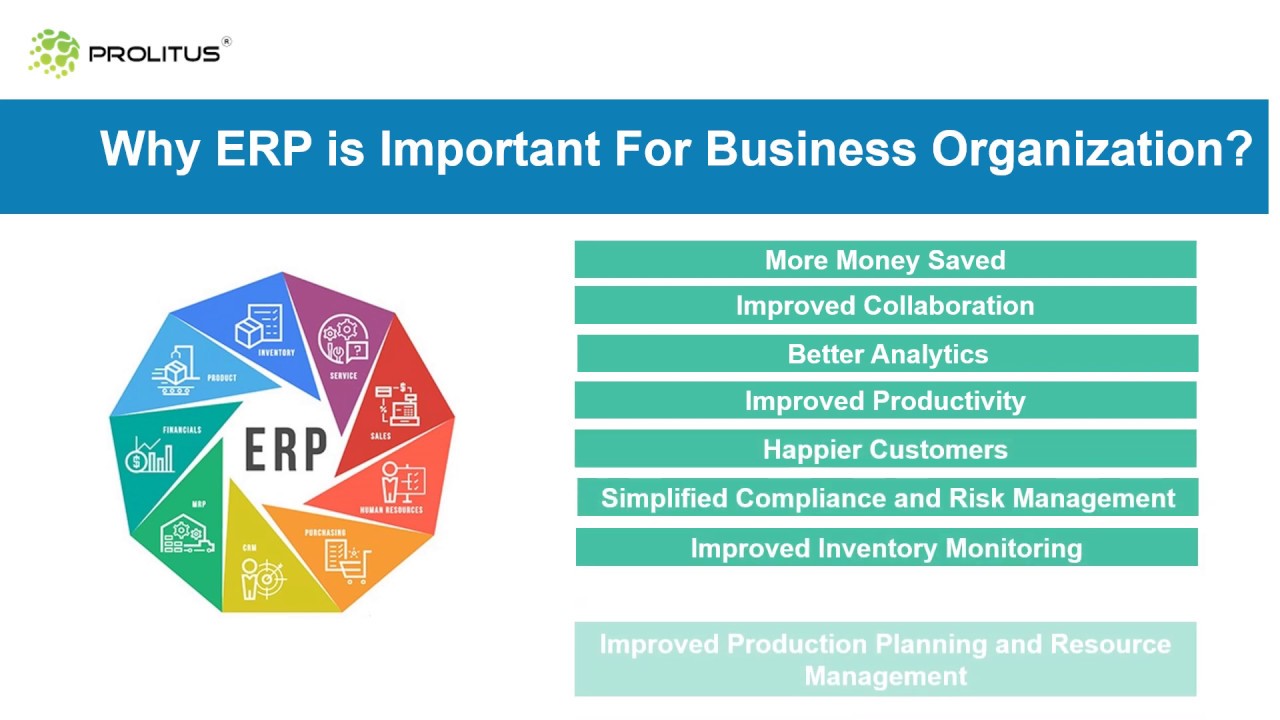
ERP systems are not merely transaction processing engines; they are powerful data repositories capable of providing invaluable insights into a business’s performance. The comprehensive data collected within an ERP system forms the foundation for robust data analytics, enabling businesses to make data-driven decisions that optimize operations and drive growth. This section will explore how ERP facilitates data analysis and its impact on forecasting, planning, and strategic decision-making.
ERP systems facilitate data collection and analysis by centralizing data from various business functions. This integrated approach eliminates data silos and inconsistencies, providing a single source of truth for reporting and analysis. The system automatically captures and records transactional data, such as sales orders, inventory levels, production schedules, and financial transactions. This data is then structured and readily accessible for analysis through built-in reporting tools or integration with external business intelligence (BI) platforms. The ability to easily query and manipulate this data allows for the identification of trends, patterns, and anomalies that would be impossible to detect with disparate data sources.
Data Analytics for Improved Forecasting and Planning
Effective forecasting and planning are crucial for business success. ERP systems leverage historical data and advanced analytics to create accurate forecasts for sales, demand, and resource allocation. For example, by analyzing past sales data, seasonality, and market trends, an ERP system can predict future demand for products. This allows businesses to optimize inventory levels, avoid stockouts, and reduce carrying costs. Similarly, by analyzing production data, capacity constraints, and resource availability, an ERP system can assist in developing realistic production plans that minimize delays and maximize efficiency. Advanced forecasting techniques, such as machine learning algorithms, can be integrated with ERP systems to further enhance forecasting accuracy. A company like Amazon, for example, relies heavily on data analytics integrated with its ERP system to predict consumer demand and optimize its vast supply chain.
Data-Driven Insights for Better Strategic Decision-Making
Data-driven insights derived from ERP systems are essential for informed strategic decision-making. By analyzing key performance indicators (KPIs) and identifying trends, businesses can gain a deeper understanding of their strengths and weaknesses, enabling them to develop effective strategies for improvement. For instance, analyzing sales data by region, product, and customer segment can reveal opportunities for growth and areas requiring attention. Similarly, analyzing production data can highlight inefficiencies in the manufacturing process, leading to process optimization and cost reduction. The insights gained from ERP data analytics empower businesses to make proactive adjustments to their strategies, adapt to changing market conditions, and gain a competitive advantage.
Key Performance Indicators (KPIs) Trackable via ERP
The ability to track and analyze KPIs is a significant benefit of using an ERP system. A wide range of KPIs can be monitored, providing a comprehensive overview of business performance. These KPIs offer real-time visibility into operational efficiency and financial health.
Why Every Business Needs ERP Software in 2025 – Here are some examples of key performance indicators that can be tracked via an ERP system:
- Sales Growth: Tracks the increase or decrease in sales revenue over time.
- Customer Acquisition Cost (CAC): Measures the cost of acquiring a new customer.
- Customer Lifetime Value (CLTV): Estimates the total revenue generated by a customer over their relationship with the business.
- Inventory Turnover Rate: Indicates how efficiently inventory is managed.
- On-Time Delivery Rate: Measures the percentage of orders delivered on time.
- Production Efficiency: Tracks the output per unit of input in the production process.
- Gross Profit Margin: Shows the profitability of sales after deducting the cost of goods sold.
- Return on Investment (ROI): Measures the return generated from investments in the business.
- Days Sales Outstanding (DSO): Indicates the average time it takes to collect payments from customers.
- Employee Turnover Rate: Tracks the rate at which employees leave the company.
Security and Scalability in ERP Systems
In today’s dynamic business environment, selecting an ERP system requires careful consideration of not only its core functionalities but also its inherent security and scalability. These factors are crucial for ensuring the long-term viability and success of any business utilizing such a system. A robust and adaptable ERP solution safeguards valuable data and allows for seamless growth and adaptation to evolving market demands.
Data security is paramount in any ERP system. Modern ERP solutions employ a multi-layered approach to protect sensitive business information from unauthorized access, use, disclosure, disruption, modification, or destruction. This includes robust authentication and authorization mechanisms, encryption of data both in transit and at rest, regular security audits, and proactive threat monitoring. Data integrity is maintained through rigorous validation checks, version control, and backup and recovery procedures, ensuring data accuracy and reliability. Compliance with industry regulations, such as GDPR and HIPAA, is also a key aspect of modern ERP security features, ensuring adherence to legal and ethical standards.
Data Security Measures in ERP Systems
ERP systems employ a range of security measures to protect sensitive data. These include role-based access control (RBAC), which limits user access to only the data and functionalities relevant to their roles, multi-factor authentication (MFA) to enhance user verification, and intrusion detection and prevention systems (IDPS) to monitor for and respond to malicious activity. Regular security audits and penetration testing help identify and address vulnerabilities before they can be exploited. Data encryption, both at rest and in transit, protects data from unauthorized access even if a breach occurs. Furthermore, robust data loss prevention (DLP) mechanisms are incorporated to prevent sensitive data from leaving the system without proper authorization. For instance, an ERP system might prevent a user from downloading a client’s financial data to a personal device without appropriate approvals.
Scalability and Adaptability of ERP Solutions
Modern ERP solutions are designed with scalability in mind, allowing businesses to easily adapt to changing business needs and growth. Cloud-based ERP systems, in particular, offer exceptional scalability, allowing businesses to seamlessly increase or decrease computing resources as needed. This eliminates the need for significant upfront investments in hardware and infrastructure. Furthermore, modular design allows businesses to select and implement only the modules they need, adding more as their requirements evolve. For example, a small business might start with core modules for finance and inventory management and later add modules for CRM or manufacturing as it grows. This flexibility allows businesses to avoid overspending on unnecessary functionalities and to adapt to changing market demands.
Adapting to Changing Business Needs
The ability of an ERP system to adapt to changing business needs is critical for long-term success. This adaptability manifests in several ways. First, many modern ERP systems offer customizable workflows and reporting capabilities, allowing businesses to tailor the system to their specific processes. Second, the ability to integrate with other business applications, such as CRM and e-commerce platforms, enhances the ERP system’s overall functionality and allows for a more holistic view of the business. Third, regular updates and upgrades from the ERP vendor provide access to new features and functionalities, ensuring the system remains relevant and effective in the face of technological advancements. For example, an ERP system might receive an update that integrates with a new payment processing platform or adds support for a new accounting standard. This ongoing adaptation ensures the ERP system remains a valuable asset for the business throughout its lifecycle.
Return on Investment (ROI) of ERP Systems
Implementing an Enterprise Resource Planning (ERP) system represents a significant investment for any business. However, the potential return on that investment (ROI) can be substantial, significantly impacting profitability and long-term growth. Understanding how to calculate and project this ROI is crucial for justifying the expenditure and ensuring successful implementation.
Quantifiable Benefits Resulting from ERP Implementation
ERP systems offer a wide array of quantifiable benefits. These improvements translate directly into increased efficiency, reduced costs, and improved revenue streams. By meticulously tracking these metrics before and after implementation, businesses can accurately assess the financial impact of their ERP investment.
- Reduced Operational Costs: Streamlined processes, automated tasks, and minimized manual data entry lead to significant reductions in labor costs and operational overhead. For example, a manufacturing company might see a 15% reduction in administrative staff after implementing an ERP system that automates inventory management and order processing.
- Improved Inventory Management: Accurate real-time inventory tracking minimizes stockouts and overstocking, reducing storage costs and minimizing the risk of obsolete inventory. A retail company could experience a 10% reduction in inventory holding costs by optimizing stock levels with an ERP’s integrated inventory management module.
- Increased Sales and Revenue: Improved order fulfillment, enhanced customer service, and better supply chain visibility can lead to increased sales and revenue. A distribution company might see a 5% increase in sales due to faster order processing and improved customer responsiveness facilitated by the ERP system.
- Enhanced Productivity and Efficiency: Automation of repetitive tasks frees up employees to focus on higher-value activities, boosting overall productivity. A marketing agency might observe a 20% increase in employee productivity after implementing an ERP system that streamlines project management and resource allocation.
Calculating the ROI of an ERP System
Calculating the ROI of an ERP system involves comparing the total costs of implementation against the total benefits realized over a specific period. This calculation helps determine the financial viability of the investment.
ROI = (Total Benefits – Total Costs) / Total Costs
Total costs include software licensing fees, implementation costs (consulting, training, data migration), hardware upgrades, and ongoing maintenance fees. Total benefits encompass all quantifiable improvements, such as reduced operational costs, increased revenue, and improved efficiency, expressed in monetary terms.
Long-Term Costs and Benefits of ERP Implementation
While the initial investment in ERP software can be substantial, the long-term benefits often outweigh the costs. Initial implementation costs are a one-time expense, while ongoing maintenance and support costs are typically lower than the cost savings and revenue increases generated by the system. Over time, the ROI increases as the system becomes fully integrated and the benefits accumulate.
Visual Representation of ERP ROI
A simple bar graph could illustrate the ROI. The x-axis would represent time (years), and the y-axis would represent monetary value. One bar would represent the cumulative costs of ERP implementation (including initial investment and ongoing maintenance), and a taller bar would represent the cumulative benefits (increased revenue, cost savings, etc.). The difference between the two bars would visually demonstrate the positive ROI over time, showcasing how the benefits exceed the costs after a certain period. This visual would clearly highlight the increasing return on investment over the system’s lifespan.
Choosing the Right ERP Solution for Your Business: Why Every Business Needs ERP Software In 2025
Selecting the appropriate ERP system is crucial for a business’s success. A poorly chosen system can lead to integration difficulties, operational inefficiencies, and ultimately, financial losses. Conversely, a well-integrated ERP system can streamline processes, improve data visibility, and drive significant growth. This section will guide you through the key considerations for selecting the right ERP solution.
Key Factors to Consider When Selecting an ERP System
Several critical factors must be evaluated when choosing an ERP system. These factors influence the system’s suitability, long-term viability, and alignment with the business’s specific needs. Failing to address these points can result in an expensive and ultimately unsuccessful implementation. The key factors include budget constraints, scalability requirements, integration capabilities, and the level of customization needed. The size of the business and its specific industry also play a significant role.
Comparing Different ERP Vendors and Their Offerings
The market offers a wide array of ERP vendors, each with unique strengths and weaknesses. A thorough comparison is essential to identify the best fit. This involves evaluating vendors based on their reputation, market share, industry experience, customer support, and the specific features and functionalities of their ERP offerings. For example, some vendors specialize in specific industries (e.g., manufacturing, healthcare), while others offer more generalized solutions. Analyzing case studies and testimonials from existing clients can provide valuable insights into a vendor’s capabilities and reliability. A direct comparison of pricing models and licensing agreements is also vital.
Evaluating and Selecting an Appropriate ERP Solution
The process of evaluating and selecting an ERP solution is iterative and requires a multi-faceted approach. It begins with a thorough assessment of the business’s current operational processes and future growth projections. This assessment informs the requirements gathering phase, where the specific functionalities and features needed from the ERP system are defined. Shortlisting potential vendors based on the requirements, followed by a detailed evaluation of their offerings through demos and proof-of-concept projects, is a crucial step. Finally, a cost-benefit analysis is conducted to compare the total cost of ownership (TCO) of different solutions against their projected return on investment (ROI).
Checklist of Questions to Ask Potential ERP Vendors
Before committing to an ERP vendor, it’s essential to ask pertinent questions to ensure the solution meets your needs. These questions should cover various aspects, including implementation timelines, training support, ongoing maintenance costs, and the vendor’s commitment to security and data privacy. A comprehensive checklist might include questions about the vendor’s experience with similar businesses, their customization capabilities, their approach to data migration, and their post-implementation support services. For instance, asking about the vendor’s experience with companies of a similar size and industry can reveal potential challenges and solutions. Similarly, inquiring about their data backup and recovery procedures is crucial for ensuring data security.
Future Trends in ERP Software
The landscape of Enterprise Resource Planning (ERP) software is constantly evolving, driven by technological advancements and changing business needs. Understanding these emerging trends is crucial for businesses seeking to optimize their operations and maintain a competitive edge in the dynamic marketplace of 2025 and beyond. This section explores key future trends in ERP, focusing on their impact on business operations and strategies for successful adaptation.
The integration of Artificial Intelligence (AI) and Machine Learning (ML) is fundamentally reshaping ERP systems. These technologies are no longer futuristic concepts but are actively enhancing core ERP functionalities, offering businesses unprecedented levels of automation, predictive capabilities, and data-driven decision-making.
AI and Machine Learning in ERP
AI and ML are revolutionizing various aspects of ERP. For instance, AI-powered chatbots are enhancing customer service by providing instant support and resolving common queries, freeing up human agents for more complex issues. Predictive analytics, driven by ML algorithms, analyze historical data to forecast future trends in demand, inventory levels, and sales, enabling proactive inventory management and optimized resource allocation. Furthermore, AI-driven automation streamlines routine tasks like data entry and invoice processing, significantly reducing manual effort and improving accuracy. Consider a large retail chain leveraging AI to predict seasonal demand fluctuations, enabling them to adjust their supply chain and staffing levels accordingly, minimizing stockouts and overstocking. This translates to substantial cost savings and improved customer satisfaction.
The Future of ERP in Industry 4.0
Industry 4.0, characterized by the convergence of physical and digital technologies, necessitates a highly integrated and adaptable ERP system. The ability to seamlessly connect and integrate data from various sources, including IoT devices, robots, and manufacturing equipment, is paramount. This interconnectedness allows for real-time monitoring of production processes, predictive maintenance of equipment, and optimized resource utilization. For example, an automotive manufacturer could utilize an Industry 4.0-ready ERP system to monitor the performance of its assembly line in real-time, identify potential bottlenecks, and make immediate adjustments to optimize production efficiency. This leads to reduced downtime, improved product quality, and increased overall productivity.
Preparing for Future Developments in ERP
Businesses need to adopt a proactive approach to prepare for future developments in ERP. This involves investing in ongoing training and development for employees to acquire the necessary skills to effectively utilize the advanced functionalities of modern ERP systems. Furthermore, fostering a data-driven culture within the organization is crucial, as effective utilization of AI and ML capabilities relies heavily on the quality and accessibility of data. Regular system upgrades and maintenance are essential to ensure compatibility with emerging technologies and to mitigate security risks. Finally, partnering with a reputable ERP vendor who offers robust support and ongoing innovation is crucial for long-term success. A forward-thinking approach to ERP implementation and continuous improvement will position businesses for success in the increasingly competitive and technologically advanced landscape of the future.
Case Studies of Successful ERP Implementations
Successful ERP implementations are not merely technical feats; they represent transformative journeys for businesses across various sectors. Understanding these success stories provides invaluable insights into best practices, potential pitfalls, and the tangible benefits achievable through strategic ERP adoption. Examining specific case studies reveals common threads that contribute to positive outcomes and helps organizations prepare for their own ERP journeys.
Numerous companies have experienced significant improvements after implementing ERP systems. These improvements span operational efficiency, financial management, and customer relationship management. By analyzing these successes, we can identify key factors contributing to their positive results and learn from their experiences.
Successful ERP Implementation at a Manufacturing Company
One notable example is a mid-sized manufacturing company that implemented an ERP system to streamline its production process and improve inventory management. Prior to implementation, the company struggled with inaccurate inventory data, leading to production delays and lost sales opportunities. The new ERP system integrated all aspects of their operations, from order processing to shipping, providing real-time visibility into inventory levels and production schedules. This resulted in a significant reduction in production lead times, improved inventory accuracy, and a substantial increase in overall efficiency. The company also reported improved forecasting capabilities, leading to more accurate production planning and reduced waste.
Improved Customer Service Through ERP Implementation in a Retail Setting
A large retail chain successfully used an ERP system to enhance its customer service and loyalty programs. The previous system lacked the capacity to effectively track customer interactions and preferences across multiple channels. The new ERP system provided a unified view of customer data, enabling personalized marketing campaigns and improved customer service. The integration of sales data, inventory levels, and customer preferences allowed the company to anticipate customer needs and provide a more seamless shopping experience. This led to increased customer satisfaction, repeat business, and improved brand loyalty.
Common Success Factors in ERP Implementations
Several common factors contribute to the success of ERP implementations. These include:
Thorough planning and preparation are crucial. This involves a detailed assessment of the organization’s needs, the selection of the appropriate ERP system, and the development of a comprehensive implementation plan. Effective change management is also vital, ensuring that employees are adequately trained and supported throughout the process. Strong leadership and commitment from senior management are essential to drive the implementation forward and overcome any challenges that may arise. Finally, choosing the right implementation partner with expertise in the chosen ERP system is crucial for a smooth and successful transition.
Case Study | Industry | Key Benefits | Success Factors |
---|---|---|---|
Manufacturing Company | Manufacturing | Reduced production lead times, improved inventory accuracy, increased efficiency | Thorough planning, effective change management, strong leadership |
Retail Chain | Retail | Enhanced customer service, personalized marketing, improved brand loyalty | Data integration, robust training, continuous improvement |
FAQ Corner
What is the average cost of implementing ERP software?
The cost varies greatly depending on the size of the business, the chosen ERP system, and the level of customization required. Expect a wide range, from a few thousand dollars for smaller businesses to millions for large enterprises.
How long does it take to implement ERP software?
Implementation timelines vary significantly, ranging from a few months for smaller projects to over a year for complex implementations. Thorough planning and a dedicated project team are crucial for timely completion.
What are the key risks associated with ERP implementation?
Key risks include inadequate planning, insufficient user training, data migration issues, and integration challenges with existing systems. Proactive risk management strategies are essential for successful implementation.
Can ERP systems be integrated with my existing software?
Yes, modern ERP systems offer robust integration capabilities with a wide range of software applications, including CRM, supply chain management, and other business tools. Seamless integration is key to maximizing the benefits of ERP.